Calcined Clay – Tracking Cement Decarbonization.
The Green Cement Technology Tracker which is helping to monitor decarbonization in the cement industry, has now been expanded to include the production of calcined clays – a key cement decarbonization solution.
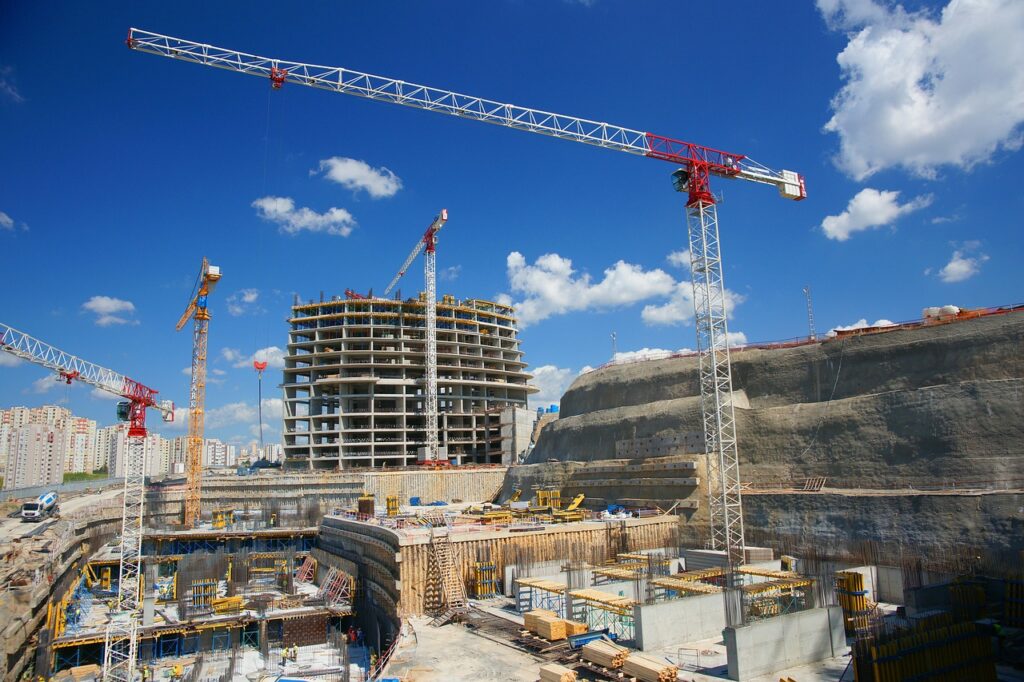
Concrete and cement are the world’s most used building materials. They are vital to the built environment for homes, offices and infrastructure, but account for around 7% of global CO2 emissions. Tracking projects which deliver emissions reductions is an important part of the roadmap to decarbonization and the Global Cement and Concrete Association (GCCA) and Leadership Group for Industry Transition (LeadIT) Green Cement Technology Tracker now includes project announcements of clay calcination kilns.
Transparency is key. In order to empower the industry and policymakers committed to emission reductions, our goal is to provide comprehensive tracking of investments in low-carbon cement production. This new addition to our trackers is extending the scope and quality.
Per Andersson
Head of Secretariat, LeadIT
The tacker, hosted by LeadIT was launched last year and already tracks carbon capture projects and pilots across the globe,. The addition of calcined clay projects broadens the tracking scope for technologies that support carbon dioxide emissions reductions in the cement sector.
The GCCA’s Roadmap to Net Zero estimates that by using calcined clays in the production of cement, instead of limestone, it is possible to reduce emissions in the production process by 11%.
Karen Scrivener, Professor at Ecole Polytechnique Fédérale de Lausanne (EPFL) in Switzerland is an expert on the use of calcined clays and was recently appointed to the United Nations SDG group. She said “Ultimately, we’re constrained by the materials we have on earth. There’s no overnight replacement to cement. However the development of calcined clays, which are widely available, offers the world an exciting opportunity to reduce CO2 emissions in cement production……we have to do all we can to decarbonise cement, whilst recognising where the demand is rightfully coming from, to improve people’s lives across the planet, including the global south.”
Driving down emissions requires investment in new technologies and production methods and incorporating calcined clay can contribute significantly making it a valuable strategy for sustainable construction.
Claude Loréa
Cement, Innovation and ESG Director, GCCA
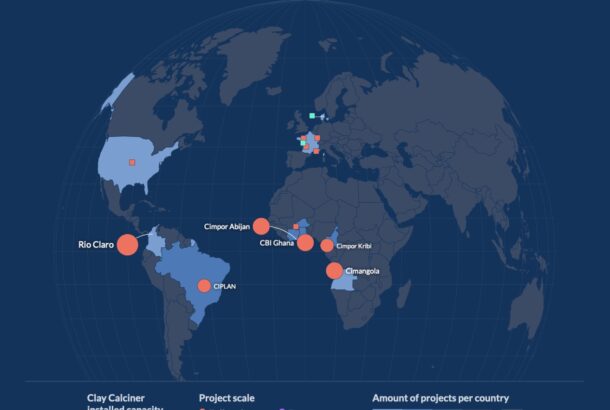
Green Cement Tracker showing Clay Calcination Kiln Projects
What are the sources of CO2 emissions in the cement and concrete sector?
During the production of cement clinker which is the main component of cement, limestone is heated in a kiln at high temperatures typically around 1450°C in a process known as calcination which releases CO2 as a byproduct. Cement is needed for the production of concrete. Additionally the energy intensive nature of cement production requires fuel, typically fossil fuels, to heat the kilns and this contributes to CO2 emissions.
What is calcined clay?
Calcined clay, also known as metakaolin, is produced by heating sources of kaolin clay (such as paper sludge) to temperatures between 650°C and 750°C. The resulting material can be added to cement as a substitute for clinker.
How does calcined clay contribute to emissions reduction?
The use of calcined clay reduces the need for clinker production which is an energy intensive process. Clinker production requires much higher kiln temperatures for calcined clay. By substituting clinker with calcined clay less energy is required leading to lower emissions. Calcined clay also releases fewer greenhouse gases when compared to the calcination of limestone.